
Precautions:
FOR PROFESSIONAL USE ONLY
- This product is not a vapor barrier. Where concrete moisture exceeds the maximum allowed, address by using Armstrong S-462 Seal Strong™ two Part Moisture Mitigation System.
- Carefully read and follow all cautions and warnings on product label.
- Never mix with cement or additives other than Armstrong approved products. Observe the basic rules of concrete work.
- Dispose of packaging and material in accordance with federal, state and local waste disposal regulations. Do not flush material down drains.
SDS
Product Information
Type | Patching, skim coating and smoothing compound |
Color | Gray |
Taggants | None |
Trowel | Smooth-edge trowel |
Thickness | From a skim coat up to ½” in interior installations over large areas, and up to any thickness in a small well-defined area such as a threshold or transition. Exterior applications may be installed at a skim coat over large areas and up to ¼” in small well-defined areas. |
Coverage | Approx. 200 – 250 sq. ft. at a skim-coat Approx. 28 sq. ft. at 1/8” |
Mix Ratio | 10 lb. bag to 1.75 quarts water 3.25 parts powder to 1-part water, by volume Do not add additional water. |
Pot Life | 15-20 minutes at 70° F |
Units | 10 lb. bag |
Shelf Life | 1 year if unopened, stored in cool, dry conditions |
Dry Time | 20 minutes as a skim coat |
VOC Content | Zero |
Clean Up | Clean tools with water frequently before material dries. Do not flush material down drains. |
Advantages | Easy to apply and achieve featheredge finish with exceptional strength No RH limit for use over concrete Suitable for use over S-462 Seal Strong™ after application of S-465 NP Prime Strong™ Zero VOC |
Language | English/Spanish/French |
Size | 10-pound bag |
Item No. | 00466100 |
Item UPC | N/A |
Carton Dimensions | 13.5″L x 9.5″W x 8.5″H |
Weight per Carton | 10.2 lbs. |
Items Carton | N/A |
Cartons per Pallet | 208 |
Warranty
Product Features
For use with the following commercial and residential applications:
- Interior and exterior patching, skim coating and smoothing of sound and solid concrete on any grade level, ceramic tile, quarry tile, and porcelain tile
- For patching, skim coating and smoothing terrazzo and burnished concrete in interior areas without excessive moisture
- Epoxy coating systems (primed with Armstrong Flooring S-465 NP Prime Strong™ Non-Porous)
- Gypsum substrates (double-primed with Armstrong Flooring S-464 Prime Strong™ Porous)
- Covering existing asphaltic cutback adhesive residue over interior concrete
- Armstrong Flooring S-462 Seal Strong™ moisture remediation (primed with Armstrong Flooring S-465 NP Prime Strong™ Non-Porous)
- Patching, repairing small voids and skim coating of approved wood underlayments and subfloors
Substrate Preparation
Concrete
All concrete must be solid, structurally sound, and clean and free of dirt, oil, grease, asphalt and latex compounds, plaster, curing compounds, sealers, polish, wax and other foreign matter that may act as a bond breaker. If such contaminants are present, mechanically remove by shot blasting or similar. Do not use acid-etching, solvents, or sweeping compounds to clean substrate. Always refer to the Armstrong Flooring Guaranteed Installation System Manual, F-5061. Completely remove any existing water-soluble adhesive and underlying patching material by mechanical means. Do not use solvents or adhesive removers. Any existing non-water-soluble adhesive must be wet-scraped down to a thin well-bonded residue. Such an adhesive must be tested to verify it is non-water-soluble and will not interact with the new flooring adhesive. The new flooring must be rated as unsusceptible to bleed through from existing non-water-soluble adhesive residue. If adhesive interaction or migration are a concern, install Armstrong S-463 Level Strong™ underlayment. Some previously manufactured asphaltic “cutback” adhesives contain asbestos. For removal instructions, refer to the Resilient Floor Covering Institute’s publication Recommended Work Practices for Removal of Resilient Floor Coverings.
Wood
Approved wood underlayments and subfloors must be deemed by the flooring installer to be securely fixed and free of undue flex. The surface of the wood must be clean and free of oil, grease, wax, dirt, varnish, shellac and any contaminant that might act as a bond breaker. Wood cleaning must be by mechanical means, such as sanding. Do not use solvents, strippers or cleaners.
Gypsum
Existing clean gypsum underlayments, deemed by the flooring installer to be sound and solid, must be prepared by double priming in accordance with Armstrong Flooring S-464 Prime Strong™ Porous data sheet instructions.
Epoxy Coatings
Existing clean epoxy coatings, deemed by the flooring installer to be sound and well-bonded, must be prepared by priming in accordance with Armstrong Flooring S-465 NP Prime Strong™ data sheet instructions.
Other Surfaces
Armstrong S-466 Patch Strong™ can be directly applied without priming over the following clean, sound and solidly bonded non-porous surfaces: terrazzo, burnished concrete, ceramic tiles, quarry tiles, porcelain tiles. The substrate must be clean, including the complete removal of existing waxes and sealers, dust, dirt, debris and any other contaminant that may act as a bond breaker. Where necessary, substrate preparation must be by mechanical means, such as shot blasting or similar.
Application Instructions
Note: While Armstrong S-466 Patch Strong™ is unaffected by water, the substrate must be dry at time of application. Substrate and ambient temperatures must be a minimum of 40°F (5°C).
Mixing and Application: Mix 10 lbs. of powder with 1.75 quarts of clean cold water. (3.25 : 1 ratio, by volume). Pot life is 15 – 20 minutes. Do not add more water. Before applying at desired thickness, initially ‘key in’ using the flat side of the steel trowel to get a good mechanical bond to the subfloor. Apply up to ½” thick on interior installations. Limit exterior installations to ¼”. Before covering with flooring, let underlayment dry for at least 30 minutes when applied as a skim coat. Complete drying time will depend on thickness.
Ready for Armstrong Flooring: Before covering with flooring, let underlayment dry for at least 30 minutes (70°F, 21°C) when applied as a skim coat. Complete drying time will depend on thickness. If installing wood flooring, or using epoxy or urethane adhesives, wait 16 hours.
Product Image
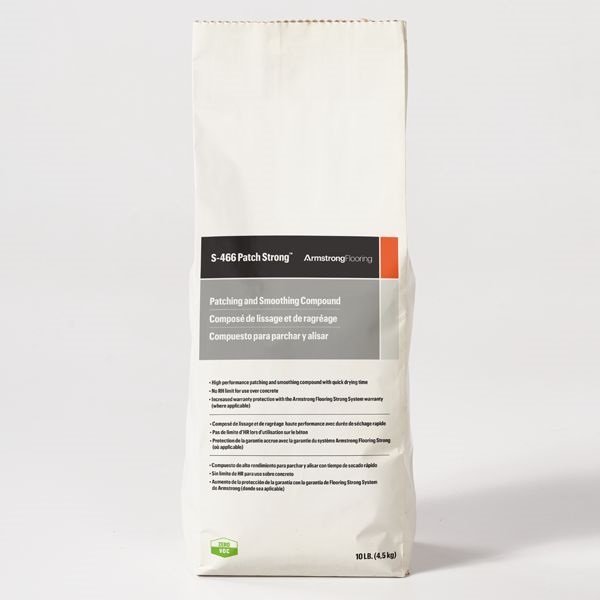
strong system